30多年來光譜科技一直處於鐳射線纜加工技術的前沿;我們開發和應用前沿技術,為先進製造業中的各種問題提供解決方案,並開創性地使用雷射技術來解決一系列問題。
本節提供了一些關於我們所開發並商業化成為我們今天產品系列的技術的背景資訊。
紫外鐳射線纜打標:解釋我們的技術
紫外鐳射線纜打標技術最初於1987年由Spectrum公司的研究人員開發,旨在滿足國際航空航太工業的需求,即在不粘PTFE/Teflon和類似線絕緣層以及光纖上安全標印識別代碼。
Spectrum公司採用的紫外鐳射打標工藝不會對線纜的機械或電氣性能造成任何損害或改變。
相比之下,舊的熱壓印方法被認為是一種具有侵略性和潛在破壞性的工藝;因此,它在SAE AS50881(以前的MIL 5088L)和類似規範所禁止。
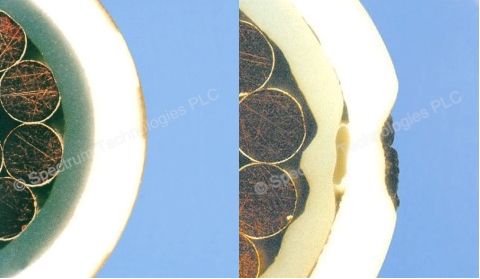
紫外鐳射線纜打標現已成為國際航空航太業廣泛接受的一種製造工藝。目前,北美和歐洲幾乎所有尖端商用和軍用航空航太專案的電氣系統製造初始階段均採用該工藝。
鐳射自 1960年問世以來,已廣泛應用於各種領域,從超市收銀台隨處可見的條碼閱讀器到家用CD播放機的“讀取”頭,再到汽車生產線上的鐳射焊接和切割設備。然而,許多人仍然將鐳射視為遙不可及的“星球大戰”技術。
實際上,雷射光束是由光組成的,光是能量的眾多形式之一。然而,與“普通”光源不同,鐳射具有一些非常特殊的特性。雖然日常光源(從太陽到燈泡)向各個方向輻射,波長範圍很廣,但鐳射的光束方向狹窄,類似於鉛筆,並且以精確和狹窄的波長(單一顏色)工作。這一關鍵差異使鐳射在用於任何性質的材料加工時具有很大的優勢,即精度和控制。
重要的是要注意,並非所有鐳射都是相同的。事實上有數百種不同的類型。然而,概括起來,我們可以將它們分為兩組:
- 波長較短的紫外(UV) 鐳射和可見鐳射:使材料能夠進行“冷”加工——無論是打標、切割還是其他加工,它們在工件中產生很少或沒有明顯的熱效應。
- 較長波長的紅外 (IR) 鐳射:主要通過熱方式與材料相互作用或處理材料,即直接加熱——非常適合焊接和切割金屬以及其他非熱敏感材料,或者用戶可接受熱副作用的材料。
因此,為特定工藝選擇正確的鐳射和波長至關重要。Spec Tech鐳射打標的線
Spectrum Technologies 開發的“冷”紫外鐳射線纜打標工藝截然不同,它基於鐳射引起的二氧化鈦(TiO2)顏料的顏色的變化。這種通常為白色的顏料已用於其他用途的航空航太電線絕緣材料。
線上纜打標應用中,紫外雷射光束通過重新排列電線絕緣層中已存在的TiO2顆粒的晶體結構(在微觀尺度上)來改變其顏色。這種重新排列在實際應用中是永久性的。這使得TiO2以及絕緣層呈現黑色,從而線上纜上形成有色或標記的表面。根據各種最終使用者進行的測試,電線沒有被燒焦,沒有顯著的材料去除,也沒有改變電線的機械或電氣性能。標記通常嵌入到大約20微米(0.0008英寸)的深度,從而提供持久的耐磨性和耐液體性
為了測試線纜標記對可能不太明顯的因素的耐久性,已經進行了將線纜樣品浸入液氮中以測試低溫(-196°C)的影響,並將線纜在其最大額定溫度或更高溫度下保持數百小時的測試。
樣品已在高達 310°C 的溫度下進行了測試,未出現不良影響。樣本還暴露於強烈的紫外線照射下,以模擬陽光長期照射的影響。
對於正確製作和標記的電線進行的幾乎所有測試都表明,標記部分沒有發生材料變化。
很能證明這一點的方法可能是將鐳射標記的線纜放入熱液壓油(如Skydrol)中浸泡24小時。取出後,對樣品進行“實際使用”測試,即在仍然濕潤的情況下立即摩擦標記的電線。經過這種測試的UV鐳射標記電線樣品均通過此測試。
結果直觀地展示了Spectrum鐳射標記相對于傳統油墨標記的持久性。
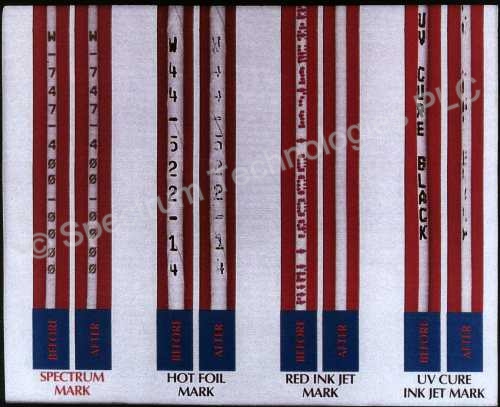
鐳射剝線:解釋我們的技術
剝線是指去除覆蓋在導電電線上的絕緣層,以便為電線的端接做好準備。
傳統的剝線技術已經發展出了機械、研磨、化學或熱學等多種方法。但每種方法都有其相關的問題,如導體損傷、加工速度慢、精度不足和品質差等。
相比之下,鐳射剝線具有快速的加工時間、出色的精度和工藝控制。最重要的是,鐳射剝線消除了與電線的接觸,並且通過使用正確的鐳射類型,可以消除導體或遮罩層受損的風險。
鐳射剝線的背景
現代電子設備以及連接它們的通信系統都充滿了電線。從用於在微波通信系統中傳輸局域網資料的巨大導體,到連接飛機和其他交通系統上所有關鍵控制和通信系統的數英里長的佈線,再到微電子系統中提供互聯或在醫療植入物中傳輸信號的微小導線,電線對於信號和電力的傳輸都是不可或缺的。
傳統的機械剝線方法使用金屬刀片切割絕緣層,使其能夠從導體末端被剝離。然而,儘管現代機械剝線設備配備了成型刀片、自動電線處理和精確的刀片控制,但它與手工剝線鉗有一個共同點:兩者都需要小心操作以避免電線受損。
歷史上,設計師和製造商不得不接受使用機械刀片剝線時對電線導體造成的一定程度的損傷。為了適應這一點,電線的電阻通常會被指定一個比實際需要的更高的公差,這實際上意味著要指定一個更大的導體;這使得整個電線更大且成本更高。
在關鍵的製造應用中,這種方法是不可接受的,當品質至關重要時,無損的鐳射剝線技術便就顯得尤為重要。對於最先進的應用來說,能夠精確地從電線上剝離絕緣層而不損傷導體是至關重要的。鐳射剝線機可以簡單地實現這一點,它依靠鐳射選擇性地去除非金屬絕緣材料,同時不影響金屬導線。
右上:鐳射剝線,同一條電纜。
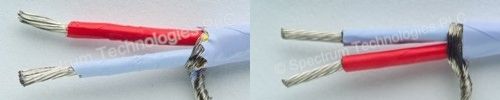
手動或半自動機械、化學或熱剝線方法存在眾所周知的品質保證問題。機械刀片是最廣泛使用的剝線工具。它最適合切割規則形狀圓形橫截面電線絕緣層;即普通的單芯線。即便如此,由於刀片磨損、刀片形狀與電線不匹配或剝線程序控制不足,也可能導致導體受損。此外,機械方法不適合剝離不規則圓形橫截面的雙絞線或遮罩電纜。
過長的處理時間和環境問題阻礙了化學剝線技術的發展。這些化學工藝通常使用熱硫酸或過氧化氫,這些物質難以使用和控制。此外,這些化學品反應性很強,需要小心處理和處置,必須充分考慮環境和現行法規。
熱剝線方法需要非常精細的工藝控制和頻繁的校準才能保持品質。熱剝線法通常還需要二次操作,以去除導體周圍剩餘的絕緣層。
相比之下,鐳射剝線具有快速的加工時間、出色的精度和出色的程序控制。最重要的是,鐳射剝線消除了與電線的接觸,通過使用正確的鐳射類型,可以消除導體或遮罩層損壞的風險。
鐳射剝線技術的發展
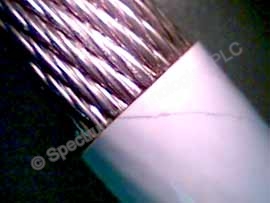
鐳射剝線的研究起源於 1976 年,當時NASA 啟動了一項計畫,開發更好的剝線方法,以克服太空梭開發過程中電線系統生產中遇到的問題。這項研究是由於需要能夠剝離飛機和航天器上使用的非常薄絕緣層的電線,為了減輕重量,通常使用非常輕且細規格的電線。他們的研究成果是第一台鐳射剝線機。
NASA 比較了各種類型的雷射器對電線絕緣和導電材料的影響,發現 CO2 雷射器是完成當前任務的最佳選擇。在鐳射剝線過程中,鐳射發射的能量或輻射被絕緣材料強烈吸收。當鐳射穿透絕緣層時,它會蒸發材料直至導體。
然而,導體強烈反射 CO2 鐳射波長的輻射,因此不受雷射光束的影響。由於金屬導體本質上是鐳射波長下的鏡子,因此該過程實際上是“自動終止”,即鐳射將所有絕緣材料蒸發到導體,然後停止,因此不需要程序控制來防止損壞導體。
自 1987 年RtMc公司(現為 Spectrum Technologies USA 公司)推出商用 CO2 鐳射剝線機以來,對進一步開發雷射技術的需求日益增加,以便能夠剝除越來越多的絕緣材料和電線類型。這是由於新型絕緣材料的發展、將絕緣材料擠壓到電線上的新方法、不同的粘合特性以及更小、更輕的電線應用趨勢,以及使用這些電線的新產品的開發。
當今的鐳射剝線技術
在此期間,Spectrum Technologies 已成為鐳射剝線的先進製造商和供應商, 已向世界各地的客戶交付了數百台設備。 Spectrum 的SIENNA TM系列鐳射剝線機是結合各種雷射器和傳輸系統而開發的,可以成功地去除電線的絕緣層。
隨著傳統剝線方法日益過時,對產品的輕量化、可靠性、效率和成本效益的需求也在不斷增加。鐳射剝線技術相比傳統方法具有許多優勢。其中一些優勢和好處包括:
- 無導體損壞——即使金屬導體上鍍有錫或銀等其他金屬,鐳射也不會損壞它——降低了品質保證要求,使設計人員能夠指定更嚴格的公差並使用更輕的電線
- 能夠處理 99% 的絕緣類型——一台設備可以加工各種電線和絕緣類型,並且可以加工一系列電線類型,而無需耗時更改設置
- 實現高品質剝線——可重複並提高產量,從而降低成本
- 能夠同時加工多根電線——提高生產率
- 能夠剝除直徑從小於 25 µm 到最大 25 m(0.001 – 1.000 英寸)的各種線徑 –支持在廣泛的線徑範圍內進行無損傷剝線
- 能夠剝除各種電線,同一台機器可以加工扁平、圓形、絞合或遮罩電纜,幾乎不需要更換工具 - 提高設備利用率和生產率
- 能夠保持+/- 25 µm(0.001 英寸)的嚴格公差 – 適用于精密應用
- 可變剝線圖案 可進行程式設計,以去除電線上任何位置的絕緣層 - 見下文
由於鐳射剝線是一種非接觸式工藝,並且可以非常精確地控制光束,因此可以引導雷射光束實現各種剝線圖案,其中許多圖案幾乎不可能通過其他方式實現,如下所示:
- 末端剝線 – 橫切或橫切和縱切
- 開窗剝線
- 迷你開窗剝線
- 斜切
- 可在電線或帶狀電纜上進行可程式設計模式剝線。
鐳射剝線可以加工以下電線電纜絕緣層:
電纜類型
鐳射剝線可以處理以下電線和電纜絕緣類型和形式:
電纜類型
- 單芯線
- 雙引線
- 雙絞線
- 多芯電纜
- 遮罩線
- 帶狀電纜
- 同軸電纜
- 複雜的 2D 和 3D 形狀導體,例如線圈
電纜尺寸
- 50 AWG (或更小) 至1 AWG
- 帶狀電纜和排線寬度可達 285 毫米(11.4 英寸)
絕緣材料
- PTFE /Teflon®
- Silicone
- PVC
- Kapton®
- Mylar®
- Kynar®
- Fiberglass
- ML
- Nylon
- Polyurethane
- Formvar®
- Polyester
- Polyesterimide
- Epoxy
- Enameled coatings
- DVDF
- ETFE /Tefzel®
- Milene
- Polyethylene
- Polyimide
- PVDF 及其它硬質、軟質或耐高溫材料
鐳射剝線實踐
在我們的主產品SIENNA 剝線機中,雷射光束聚焦成非常小的光斑尺寸,並以預設速度穿過電線。然後,鐳射汽化選定的絕緣區域,將其去除。
如前所述,鐳射不會損壞導線,因為金屬材料對 CO2 雷射光束具有高反射性,而絕緣材料通常具有高度吸收性。當光束穿過電線時,它會精確地切穿絕緣層,就像一把看不見的熱刀切黃油一樣,形成整潔的切口直到導體,使絕緣層易於去除。通過結合移動工件和光束,我們的不同產品可以根據應用的要求實現各種剝線幾何形狀,例如橫切和開視窗等。
SIENNA 鐳射剝線機既可以作為獨立設備使用,也可以作為自動化系統的一部分使用。當設備獨立使用時,導線可以批量加工,由操作員手動裝載,可以單個或成組安裝在工具板上。在需要批量加工同類型電線的情況下,安裝在工具板上可加快剝線過程並提高生產率;設置完成後,將工具板放入剝線機中,剝線機將一次或多次穿過電線,並行剝線。
或者,我們可以提供SIENNA AWH 自動線纜處理系統來實現自動化,該系統作為集成設備的一部分,將線纜從線卷自動送入剝線機。通過這種方式,可以通過 SIENNA 系統控制器自動批量處理作業。對於更高水準的自動化,我們的產品也可供系統集成商使用,他們可能需要將它們集成到更複雜的自動化系統中。
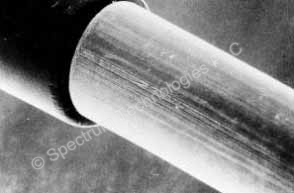
為了方便使用 SIENNA 剝線機,Spectrum Technologies 提供了一系列輔助設備,包括控制系統、冷卻器和空氣淨化裝置,以便根據每個客戶的需求提供完整的交鑰匙解決方案。
當雷射光束與有機材料相互作用時,通常會產生煙霧和顆粒,必須將其從設備附近清除。為此,我們可以提供 ACS -5用於空氣抽取和淨化,適用於所有 SIENNA 設備。或者,如果客戶有合適的通風和過濾系統,可以將 SIENNA 剝線機的排氣口直接連接到這些系統上。
對於某些應用,我們需要使用其他類型的鐳射,以處理更難去除的絕緣類型或更小線徑的線纜。
如果我們的SIENNA 產品不能滿足您的需求,我們將很樂意與您討論您的應用。我們可以在我們的應用實驗室中進行工藝評估和開發,如果合適的話,我們可以相應地定制系統(見下文)。
未來的發展和應用
所有市場領域都在不斷出現新的技術發展和創新。新產品開發的進步正在改變設備或元件的功能、外觀和通信方式。隨著這些新進展的出現,這些設備的佈線也在不斷變化:電路變得更小、更快,而電線製造商也在開發新的絕緣材料、更小直徑的電線以及能夠超越以往性能的新型電纜和電線。隨著材料和組件設計的進步和尺寸的縮小,它們需要改進的製造工藝,以確保保持更高的產品品質,同時降低生產成本。
隨著產品變得更輕、更可靠、更高效和更具成本效益,傳統的剝線方法已越來越過時和不可接受。無論是對電線的損壞、需要不斷監控刀片以確保品質標準,還是更換零件的成本高昂,設計師和製造商都發現他們需要找到這些方法的替代方案。
Spectrum Technologies 專注於提供基於雷射技術的解決方案,用於去除金屬線或光纖等絕緣材料,以及先進製造中的其他應用。隨著我們繼續研究和開發新的鐳射加工技術及其應用,如果您有任何無法用我們的標準產品解決的問題,請隨時與我們聯繫。
光譜鐳射設備廣泛應用於各行各業和各種不同的應用中。
下面您將看到一些示例,說明我們的產品可以在哪些情況下使用。如果您訪問我們的線纜樣品庫,您將找到一系列使用SIENNA鐳射剝線設備剝除的線纜樣品照片。
如果您的鐳射應用未在這些頁面上列出,並且希望我們提及,請聯繫我們.
您還可以使用網站右上角的搜索框搜索特定類型的線纜。
電線/電纜標印
Nova鐳射和NovaJet噴墨線纜打標系統提供高品質、永久且高度清晰的線纜標識。我們有一系列產品可以滿足所有產量要求,以及自動化配件以最大化生產效率。
- 入門級生產或低產量、MRO:Nova 50-100i系列
- 低產量生產: Nova 800
- 中等產量生產:Nova 820; Nova 840
- 高產量生產: Nova 860; Nova 880
- 線纜處理與自動化
電線/電纜剝線
SIENNA紅外二氧化碳鐳射剝線系統,採用線性、單軸或雙軸或旋轉光束傳輸配置,可剝離大多數電子製造應用中使用的線纜。
電線/電纜外徑小於 7 毫米(0.04 英寸)*:
- 固定軸 (在x-y移動平臺下方移動 - 4類鐳射):SIENNA 225FB
- 僅末端剝線: SIENNA 210S; SIENNA 325S; SIENNA 350S
- 末端剝線和開窗口剝線:SIENNA 210D; SIENNA 325D; SIENNA 350D
- 快速、更精確的剝線:SIENNA 725D; SIENNA 750D
電線/電纜外徑大於 7 毫米(0.04 英寸)*:
- 剝線長度高達 200mm (7.9″): SIENNA 530 和 SIENNA510
自動化鐳射剝線、測量與切割
SIENNA 700線纜剝線機可以自動化執行剝線、測量和切割操作。這是通過將鐳射剝線的快速、無損精度與機械測量和切割系統的便捷和高效相結合來實現的。
- 可提供 SIENNA 200AWH 和SIENNA300AWH
電纜遮罩層切割
SIENNA線性雙軸和固定軸剝線系統用於切割微型或同軸電纜元件中的金屬遮罩層。雷射器會在遮罩層上劃一條線,然後可以輕鬆將其折斷並移除以暴露下面的電介質。
- 固定軸(在x-y移動平臺下方移動 - 4類鐳射): SIENNA 220SRFB
- 僅末端剝線: SIENNA 220SRD
- 末端剝線和開窗口剝線: SIENNA 220SRD